Drum granulator
- Power: 5,5 – 37 kW
- The size of the particles: 3 – 6 mm
- The degree of granulation: 90% +
- Production capacity: 1 – 30 subject.
- The size of the particles of raw materials before granulation: 50 oven.
- Moisture content of raw materials before granulation: 20% – 40%
- Equipment material: Carbon steel Q235, Rubber material lining
- Application: Manure animals, The remains of biogas, humus, brown coal, NPK, bentonite, Mineral fertilizers…
Drum granulator also called a drum granulator, which is suitable for granulizing organic fertilizers or complex fertilizers. How it worked for you? First you serve the material through the port port. Materials, which you add, will be turned into granular fertilizer under the influence of a special structure inside the cylinder. The final finished granular fertilizer will flow out of the final opening. The continuous operation of the drum granulator will allow you to implement mass production.
The speed of forming balls of the drum granulator can reach 70%. Even if some granules do not meet your requirements, You can use crushing equipment, such as Vertical crushers, to grind them and re -granate, To reduce the amount of waste.
How much high -quality organic granular fertilizer can produce a granulator drum per hour for you?
The performance of our drum granulator is 1-30 T per hour, Different models can produce different performance for you per hour. at present. We have five popular models of drum granulators, who are very popular among customers. This is SXZGZ-1240, SXZGZ-1560, SXZGZ-1870, SXZGZ-2080, SXZGZ-3210, These five drum granulators.
If your production need is 1-3 subject, We recommend that you choose the drum granulator SXZGZ-1240, which can fully satisfy your needs and consumes everything 5,5 kW. The performance of the drum granulator SXZGZ-1560 is 3-5 subject. If you have a small factory, You can choose this. Consumes 11kW per hour.
If your plant is positioned as a medium -sized plant, then our drum granulator SXZGZ-1870 will be a good choice for you. He can produce for you 5-8 tons in time, Consuming only 15 kW. There is also a drum granulator with a capacity of 8-15t/h, Model SXZGZ-2080, Power consumption 18.5 kW. It is also ideal for large -scale production in your medium -sized business.
If you are a major factory, We recommend that you choose the latter, Drum granulator SXZGZ-3210. He can produce for you 15-30 tons per hour and consume 37 kW.
What methods can help you control the size of the particles, produced by the drum granulator?
Correct the properties of raw materials:
Input raw particles size directly affects the size of the particles of the final product. The smaller the particles of raw materials, all the easier to mold products with small particle sizes.
The moisture content of raw materials It is also very important. Correct humidity can strengthen the power of the connection between the particles of raw materials and help small particles aggregate into larger particles.
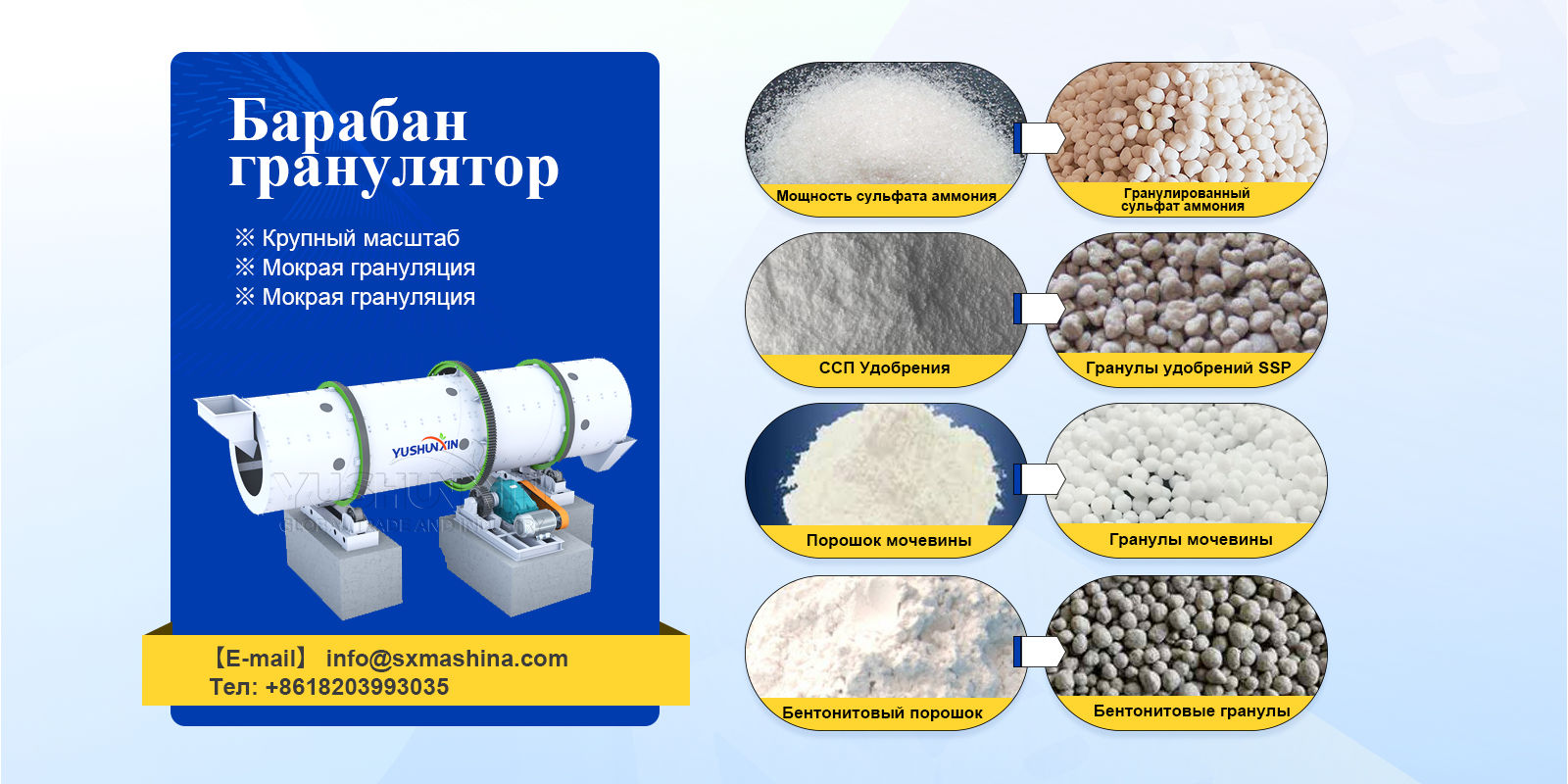
The parameters of the control drum:
Adjustment The speed of rotation of the drum allows you to change the rate of particle formation and collision intensity between particles. When rotation speed is higher, the force of the collision between the particles increases. This can lead to fragmentation of small particles or accelerated aggregation between particles, As a result, smaller particles are formed. When the drum rotates slowly, particles have more time for growth inside the drum, forming larger particles.
Change the angle of tilt of the drum, to set up trajectory and the time of stay of the material in the drum. When the angle of inclination is larger, the time of stay of the material is shorter and the smaller particles are usually formed. The smaller the angle of inclination, the longer the time of stay, which contributes to the formation of larger particles.
Optimize the internal structure of the drum (For example, lifting plates, Partitions, etc.. e in.), To change the stream mode and mixing materials. The lifting plate can improve the mixing effect and the frequency of the circulation of materials, and also contribute to the uniform formation of particles. Partitions can share various areas inside the drum, influencing the flow of materials and the growth of particles.
What granulation process is used in our drum granulator, To help you produce high -quality organic granular fertilizers?
Our drum granulators use for you the process of wet granulation. Adding a binder and rotating cylinder. As a result, pressure will be created between the particles of the material, and they will be agglomerated in balls and, finally, make a high -quality organic granular fertilizer for you. The binder may be water or steam. You can add a binder before the start of granulation or after, how the material gets into the drum granulator.
How the binder is added after, how the material enters the drum granulator?
On one side of the input opening of the drum granulator will be a tank with a coating, containing additives. The pipe will transport additives from the tank for applying the coating to the loading opening of the granulator. This pipeline is usually equipped with a pump or other pressure device for regulating the flow rate and glue supply speed.
Inside the eardrum at the end of the pipe, a sprayer or nozzle will be installed. These devices are equipped with accurate dispersal holes or nozzles tips, which allow you to regulate the spray angle and pressure. When the material enters the drum through the feed hole, The internal spray is evenly spraying the glue to the surface of the material.
What special production processes are used in the production of our drum granulator, To help you reduce equipment losses?
For facing the drum of the drum granulator, we have two options: Facing with polyethylene rubber with ultra -high molecular weight UHMW-OR, And the other – Conducting with acid -resistant stainless steel. They can be chosen in accordance with your needs.
To prevent the reverse flow and leakage of the material, We installed stop rings for you at both ends of the drum granulator. Stop ring at the exit from the eardrum can not only increase the thickness of the material in the cylinder, but also extend the time for you to stay material in the drum granulator, So the finished granular fertilizer, which you will receive, will be more beautiful.
How to serve a drum granulator, to extend the service life of your drum granulator?
Before starting the car, lubricate the gear of the drum granulator with yellow dry oil. The drum granulator gearbox also needs to be filled once before use by transmission oil, And you need to change it every four months. On the surface of the belt of the drum granulator, it is necessary to apply yellow dry oil once every seven days, And the bearing nest should be painted with yellow, dry oil every three months or replaced with new yellow dry oil.
Compliance with the foregoing may extend the service life of your drum granulator, reduce equipment loss and, Thus, reduce production costs.
Some general problems of the drum granulator and their solutions.
· The case of the machine is not leveled.
If this problem arises, it is necessary to check the supporting and holding wheels. Repair or replace it depending on the degree of wear.
· The gears are shifted.
Under normal conditions, this problem has two reasons: One of them is The wear of the small gear, and the other is damage to the connection between the large gear and the cylinder. You need to check them one by one. If this is the cause of the gear, You need to install the gear in the reverse order, when both sides are worn out, You need to replace it with a new. If this is a connection problem, You need to deal with her.
Whether we provide individual services for the manufacture of a granulation line with a rotating drum?
Of course there is. You can tell us your production needs, Initial capital, location, etc.. e. We will design for you the most suitable line for the production of granulators. We will do our best, To reduce the project cycle and complete the production and installation of all equipment on the production line as soon as possible, so that you can open your business as soon as possible.
If you want to produce granular fertilizers of a higher concentration, We recommend that you equip disk granulator, If your budget is sufficient. Connect the drum granulator with a disk granulator sequentially for secondary granulation, Increase production efficiency and fertilizer quality.
The Russian customer ordered the SXZGZ-3210 drum granulator for the production of limestone granules.
Like a company, specializing in providing solutions for pellet production. Recently, we have successfully delivered the Russian customer to the drum granulator of limestone sxzgz-3210. Used for the production of high -quality limestone granules. This Russian client is a well -known local company for the production of building materials, specializing in the production and sale of limestone particles. Since market demand continues to grow, company needs to increase the efficiency of its production lines and product quality. Due to the demand for high performance, customers chose drum granulators between drum And disk granulators. Model SXZGZ-3210, production capacity 15-30 subject.
Our drum granulator SXZGZ-3210 has gained recognition of customers due to its excellent performance and stable working condition. It can produce limestone particles with a homogeneous particle size and high strength. Match the strict requirements of customers to product quality. The customer was very pleased with the operation of the equipment from the moment of its installation and commissioning. They especially appreciated the simplicity of operation and equipment performance. The reviews said, that new equipment helped them significantly increase productivity and product quality. Successfully satisfying the growing market needs.
Frequent questions about the drum granulator!
At fertilizer production drum granulator Suitable for the production of complex fertilizers of cold, hot and low, medium and high concentration. Hot and cold granulation process The drum granulator refers to two methods of forming granules of fertilizers under different temperature conditions. These two methods have different applications and advantages in the production process:
Drum granulator of cold granulation
Cold granulation in the production of fertilizers is a granulation process at room temperature. This method does not require the heating of the material. For the formation of particles, it is mainly based on mechanical force and binder material.
Features include:
- 1
Suitable for heat -sensitive materials: Some ingredients can decompose or lose activity at high temperatures, Therefore, cold granulation can maintain the effectiveness of these ingredients.
- 2
Energy saving: since heating is not required, Energy consumption is low.
- 3
Suitable for simple processes: usually used to produce some fertilizers, not requiring strict requirements for the size of particles or strength.
Drum granulator for thermal granulation
Thermal granulation in the production of fertilizers involves heating the material to a softened or partially molten state. Then the granules are formed using the drum -granulation mechanism.
Features of this process include:
- 1
Improved pellet quality: With thermal granulation, more rounded, dense and durable pellets. Increasing the efficiency of fertilizers.
- 2
Better suited for certain chemical reactions: Some types of fertilizers require chemical reactions at high temperatures to increase their effectiveness or stability.
- 3
Fast drying: since the granules are formed at high temperatures and the moisture content is reduced, The subsequent drying process can be reduced.
The choice between cold or hot granulation usually depends on such factors, as requirements for the final product, characteristics of raw materials and production costs. For example, In complex fertilizers (Such as nitrogen, phosphorus and potassium complex fertilizers) The process of thermal granulation is often used, to ensure the uniformity and stability of particles. Some organic fertilizers may be subjected to cold granulation to protect the activity of organic ingredients.